Judging whether a car is good or not, in addition to the cooperation of "throttle" and "brake", the steering system accounts for half of the score. The so-called car handling, mainly depends on whether the steering wheel has reached the level of "people and vehicles in one". From the steering wheel to the front wheel, the process of steering requires a systematic translation and delivery.
This article refers to the address: http://
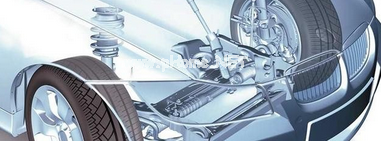
In this article, we will interpret the steering system of a car to explore why such technology can have such a large impact on the driving feel of a car, and even directly determine the attributes of a brand.
To understand the turn, we must first understand a basic common sense, that is, turn to help. The response speed, accuracy and strength of the steering system are directly related to the steering assist system. It is not difficult to understand that due to the huge friction between the two tires on the front wheel and the ground, the human arm must overcome this force to complete the steering, which will be very tired, affecting the driving experience, and is not conducive to the safe situation of emergency avoidance and other safe situations. .
Therefore, the existence of power is very necessary. In general, the source of energy for steering assistance is the engine belt. According to the specific implementation form, the steering assist is divided into hydraulic assist and electric assist. Subdivided, hydraulic power is divided into mechanical hydraulic power and electric hydraulic power; while electric power means the pull and power of the steering rod are all executed by the motor, without the application of hydraulic principle.
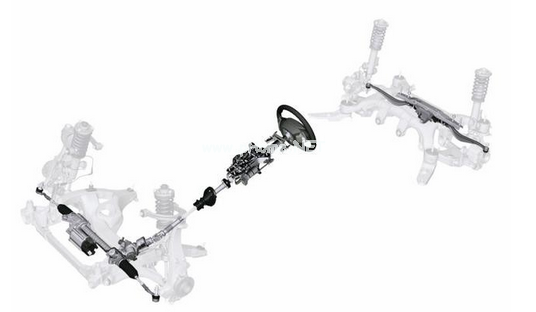
Electro-hydraulic boost is an upgraded version of mechanical hydraulic boost that makes the boost even more powerful, the steering wheel is lighter, and the power of the boost can be adjusted. But compared to electric power, electro-hydraulic power is still relying on hydraulic principles to achieve energy transfer. The electric booster gives up the hydraulic principle and is directly responsible for the steering pull and providing assistance.
Compared with the former, the electric power steering is more precise, and there is no error like hydraulic power. At the same time, since the entire steering system is electronically and digitally, the steering force is adjusted more accurately. In winter and summer, the flexibility and response speed and accuracy of the steering system are not affected by the physical properties of the hydraulic fluid.
This is a boost. A steering shaft mechanism from the steering wheel to the front wheel also requires a steering shaft. This part is responsible for communicating direction and strength to the drawbar and booster mechanism. The difference in handling between the various car brands is mainly due to the "translation" of the steering wheel.

When it comes to handling, everyone’s evaluation of BMW is very high. In fact, in the models I have tested, BMW's steering system is the most "one person and one" feeling. In other words, BMW's turn has always been a "thief", and it is sensitive to the rotation of the steering wheel. Coupled with the assistance of electric power, the steering wheel controls the front wheels very accurately and quickly.
In addition, due to the insistence on the rear drive, the front and rear weight ratio of the BMW model is generally 50:50. This makes the body have a good follow-up. This is why people talk about BMW's control. To be honest, if I go from the perspective of "throttle" and "brake", I personally think that Volvo is better than BMW.
In the short term, there seems to be no major improvement in steering assistance. So the car companies put their attention on the steering shaft. The most prominent change in this regard is the steer-by-wire, Drive by wire. The Infiniti Q50 is the first model to apply this technology to production cars.
The steer-by-wire steering eliminates the mechanical connection between the steering wheel and the front steering mechanism and is replaced by a digital steering system. Let's take the Q50 DAS steering system as an example to understand the principle of steer-by-wire steering.
As can be seen from the above figure, the Q50 still retains the traditional mechanical steering assembly, but has a clutch (silver cylinder) in the middle. The function of this component is that when the remote steering fails, the mechanical steering can be connected to ensure that the steering system is still available.
The three silver boxes on the left are three sets of ECUs (electronic control units) that handle the turn signals, and each ECU can “translate†the steering wheel commands individually. Connected to the lower end of the ECU are three sets of motors that perform steering tasks. Two groups of motors are responsible for steering, and the third group of motors is responsible for simulating road feel.
In the driving experience, the Q50's DAS system is very directional, and the simulation of the road feel is also in place. If it is not specifically stated, it is not much different from an ordinary mechanical steering model. However, when you turn on the adaptive battery life and lane keeping system, when driving a road with a certain curvature, the front wheel is cheaper at a small angle, but the steering wheel remains still.
Wire-controlled steering is a major technological upgrade based on electric power steering, and its significance is equivalent to technical iterations from analog signals to digital signals. The advent of the DAS also means that the military technology applied to the fighter aircraft was officially transplanted to the civilian car.
Not only steering, but also the remote control technology can be applied to other transmissions of the vehicle, such as the rear drive and the drive shaft of the four-wheel drive. The sensor is used to detect the torque distribution of the front axle, and the onboard computer determines how much torque is distributed to the rear axle, and then the ECU is responsible for notifying the motor of the rear axle to complete the torque distribution. In this way, there will be no high protrusions in the middle of the rear seats.
KNL1-100 Moulded Case Circuit Breaker is MCCB , How to select good Molded Case Circuit Breaker suppliers? Korlen electric is your first choice. All moulded Case Circuit Breakers pass the CE.CB.SEMKO.SIRIM etc. Certificates.
Moulded Case Circuit Breaker /MCCB can be used to distribute electric power and protect power equipment against overload and short-current, and can change the circuit and start motor infrequently. The application of Moulded Case Circuit Breaker /MCCB is industrial.
Korlen electric also provide Miniature Circuit Breaker /MCB. Residual Current Circuit Breaker /RCCB. RCBO. Led light and so on .
KNL1-100 Residual Current Circuit Breaker
KNL1-100 Molded Case Circuit Breaker,KNL1-100 Small Size Molded Case Circuit Breaker,KNL1-100 Electrical Molded Case Circuit Breaker,KNL1-100 Automatic Molded Case Circuit Breaker
Wenzhou Korlen Electric Appliances Co., Ltd. , https://www.zjaccontactor.com